Static charge is rarely recognized as a contamination driver in the pharmaceutical and medical device industries. First recognized by the electronics industry as a mechanism for product damage from discharges, it has been since identified as one of the top sources for micro contamination of product in many industries, yet it is not recognized in life sciences. This mechanism is also called electrostatic attraction (ESA).
The mechanism for electrostatically driven micro contamination is straightforward. All matter is made up of positive and negative charges which are well balanced but not PERFECTLY balanced on individual microscopic particles. Thus, any charged surface will attract or repel contaminants with such force that it overcomes the cleansing effects of unidirectional clean airflow. Thus, left unchecked, electrostatically charged surfaces easily defeat the cleanroom protocol resulting in contaminated product. The surfaces effectively suck contaminants out of the air stream. Unfortunately, for those unaware of the effect (see below) end up setting higher contamination level limits for a production line than are necessary.
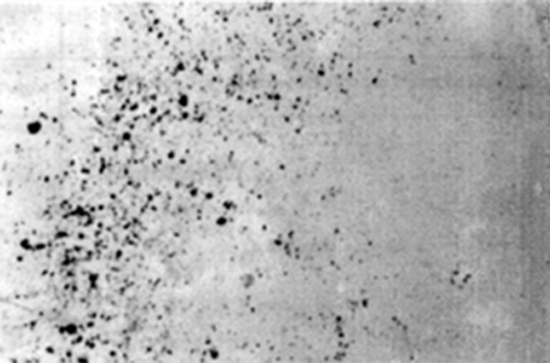
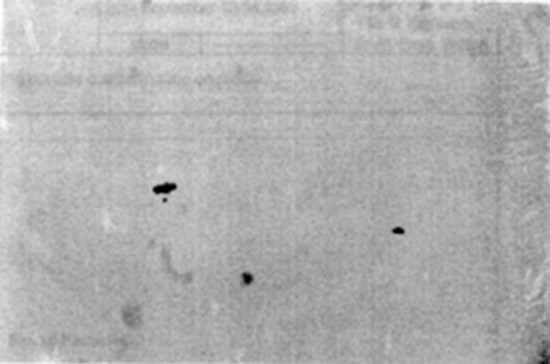
The powders used in pharmaceutical manufacturing, the walls of process equipment and the substrates of medical devices are virtually all insulators and will hold static charge indefinitely. The low humidity of a cleanroom and the movement of product through the lines are drivers for the generation of static charge. Thus, most cleanrooms exhibit 10 to 100 times greater charge levels than are experienced in everyday life in a conventional room. Greater charge level means more significant contaminating forces.
Other effects which most cleanroom operators will recognize are:
- Powders sticking to the glass or plastic containers which cannot be blown off
- Analytical balance readings having wandering zero point (owing to electrostatic forces)
- Plastic sheets sticking to a wall of to a work surface becoming impossible to remove with gloved hands
- Powders being hurled up out of a glass of plastic container as they are poured in.
Studies and computations have both shown that particles 10 um or smaller do not exhibit the same behavior as macroscopic particles in a in a conventional environment. They can easily move backward against wind and fall upward owing to the higher charge to mass ratio as compared with larger objects.
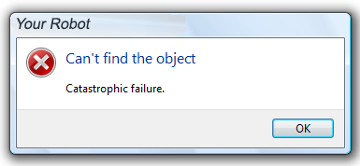
A second effect which is equally subtle is the effect of electrostatic discharge (the well-known blue sparks) on automation. These sparks create electromagnetic interference which is shorter in duration that 1 nanosecond! Robots are driven by microcomputers and their behavior is completely determined by the microcode that is executed. Static discharges are extremely fast and move easily through a cleanroom. The most efficient way that they can be absorbed is in very wide bandwidth electronics which virtually always is the microcomputer itself. An electrical pulse induced by a static discharge (transient EMI) will occasionally modify the microcode and cause the robot to exhibit strange behavior. Often, the robot will halt and display an unintelligible error message
Since this only happens occasionally (say once a day or once a week), the problem is often attributed to a fault in the robot. It often takes a year to resolve the issue, during which time, the robot will occasionally destroy product, perhaps requiring a shutdown and cleaning of the process tool. Alternately, the tool may stop and require being rebooted. This result is shut down and backup of the production line.
Microrite personnel have and use appropriate sensitive instruments to detect such problems. This allows such anomalous robot behavior to be diagnosed and mitigated.
An electrostatic audit and an electrostatic control program both involve identifying ungrounded objects in the cleanroom, and grounding them. This can be objects as mundane as shelving or carts. The program also identifies insulators like plastic ware and attempts for find alternatives. The program identifies processes which by their nature generate large charges. The last step is the implementation of air ionization to deal with the remaining charge on process required insulators and a maintenance program for ionizers. Such a program will minimize or eliminate the negative effects of static charge.